RESOURCE SHORTAGES
As the economy reopened, product demand quickly ramped up, without the resources needed to support supply chain production. At Effectus, we view the Ecosystem of Product as the network of entities that facilitate product and brand journeys. That network consists of brands/manufacturers, distributors, retailers and consumers. From a supply and demand perspective, these relationships can be seen as an assembly line that moves products through the supply chain and into the hands of consumers. However, as is the case with resource shortages, the external forces directly imposed on one player in this network often create a ripple effect for the others in the form of delays, price volatility and more. The Institute for Supply Management (ISM) found that, today, companies and their suppliers are experiencing record-long lead times, shortages of critical basic materials, rising commodities prices and transportation constraints. From the manufacturer to the consumers, the entire Ecosystem of Product has felt this pressure through some form of price increases. According to the Labor Department’s consumer price index (CPI), consumers have experienced a 5% year-over-year jump – the highest increase since summer 2008.
I. Raw Materials Shortages
Raw materials are an integral part of the global supply chain as they are the DNA for the finished goods that enter the market. The cost of raw materials can be quite volatile, making it important to understand those drivers. Some of these drivers include labor, inflationary pressure, supply and demand disruption and M&A activity. One such example that is affecting the availability of raw materials is the lack of shipping containers. Access to raw materials such as resin, a key component in developing plastic goods, has also been impacted by the political climate and ongoing trade wars, whereas the metals market has seen additional shifts in light of M&A announcements among steel and iron players. Two such transactions are set to take place in China and are considered “megamergers”. These strategic moves are giving the remaining organizations more price control over materials, and likely offering them opportunities to consolidate resources and improve profitability.
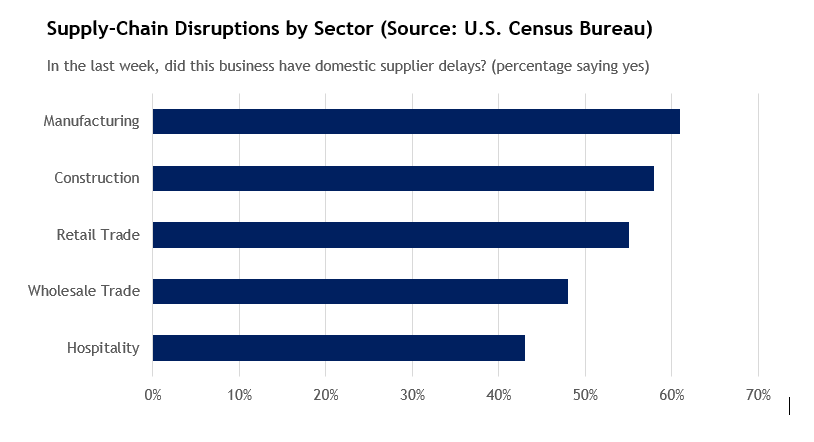
II. Freight and Shipping Cost Drivers
Over the last year and a half, supply chain logistics have been disrupted by everything from shelter-in-place regulations to the Suez Canal, which helps facilitate roughly 12% of all global trade, being blocked for several days. Delays and closures in ocean freight have made it challenging from retailers to keep up with high consumer demand. To combat this, importers are placing peak season orders earlier to avoid being out of stock during key retail seasons like back-to-school. Relative to this time last year, freight rates from Asia-US West Coast have more than doubled and Asia-US East Coast have nearly tripled. While air cargo is more expense than ocean cargo, the rates and transit times are more reliable in the face of logistics volatility. Manufacturers are looking to air cargo as a means of providing inventory to retailers and developing customer loyalty as competitors struggle to stay in stock.
Aside from freight transportation limitations, a global shortage in available shipping containers is affecting shipping costs. With labor shortages being a product of COVID-19, containers have effectively been abandoned in ports and rail yards, leaving customers unable to receive the containers needed to transport their products. Ports in South America and Africa are where many stranded containers are as these routes are less profitable.
Furthermore, labor constraints have been identified due to a lack in dockworkers, truck drivers, longshoremen and rail workers. These labor resources have made it difficult to unload vessels in a timely manner across the various freight mediums. In the case of ocean cargo, wait times for anchorage at ports has exceeded a week tying up laborers and equipment needed to pick up containers, execute voyages and keep union workers happy and healthy.
III. Ecosystem of Product Impact
Across the board, sourcing raw materials has become a pain point for many industries and companies, many of which exist in our Ecosystem of Product. As previously discussed, brands are paying a premium to expedite their products due to a lack of transit resources. In retail, consumer brands are either cutting costs or raising prices to absorb the impact of premium costs. These price increases are existing at both the brand and retail level, as seen with grocery chain Albertsons and consumer packaged goods (CPG) giant Procter & Gamble who announced price increases on products such as Pampers and Tampax.
Aside from price fluctuations, the lack of raw materials and equipment needed is translating to increased lead-times for finished products. For some brands, these delays are a matter of weeks, and for others, delays are unclear and constantly changing. Brands are making a point to be more thoughtful about purchasing by increasing shipment size, storing more supplies and replenishing inventory sooner than they normally would. This reinforces the importance of understanding and developing more accurate sales forecasts. It continues to be important to balance inventory on-hand with sales opportunities, and with the ongoing pressure of resource constraints, layering those realities into inventory and sales forecasting will be essential in our Ecosystem of Product.